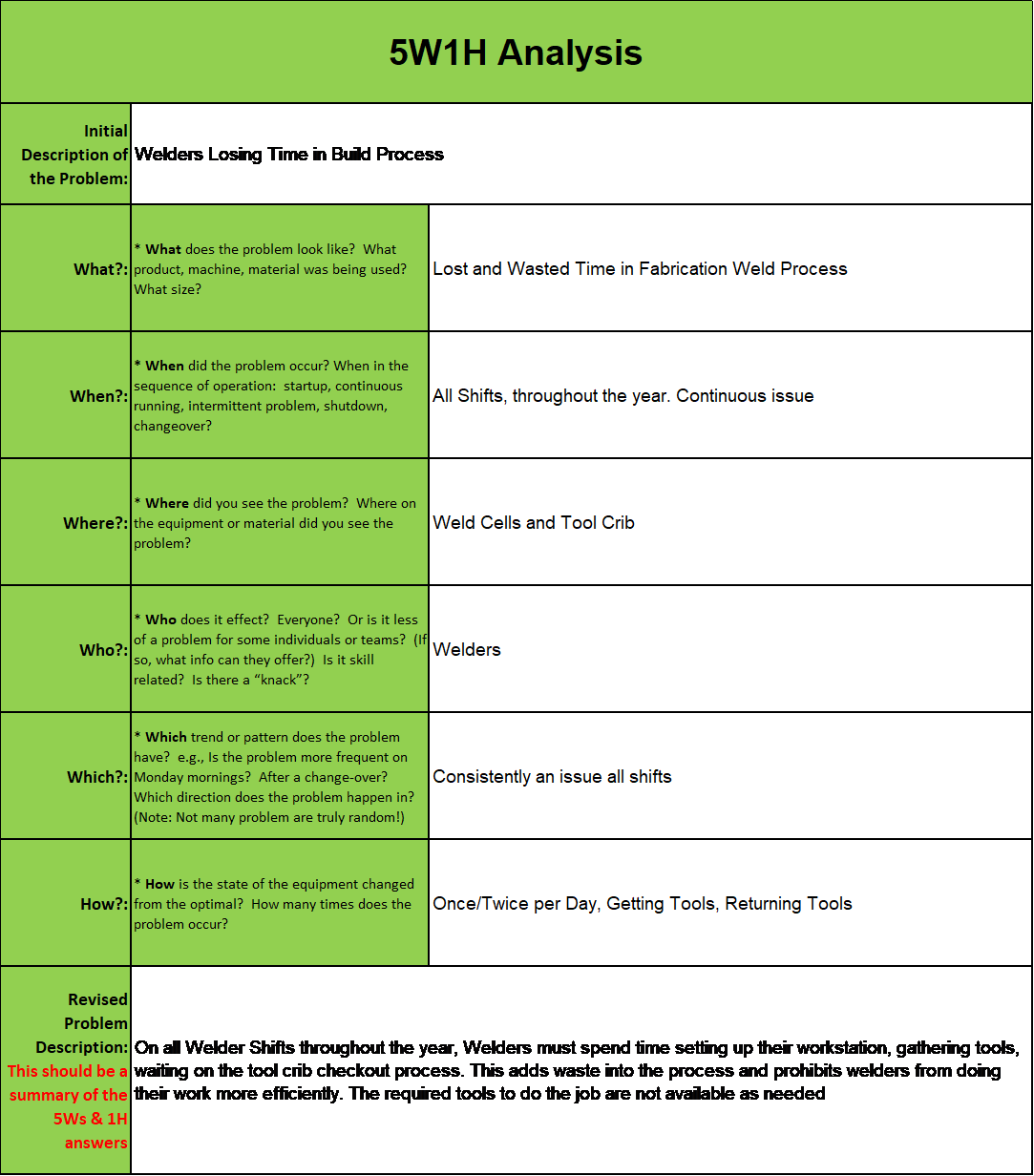
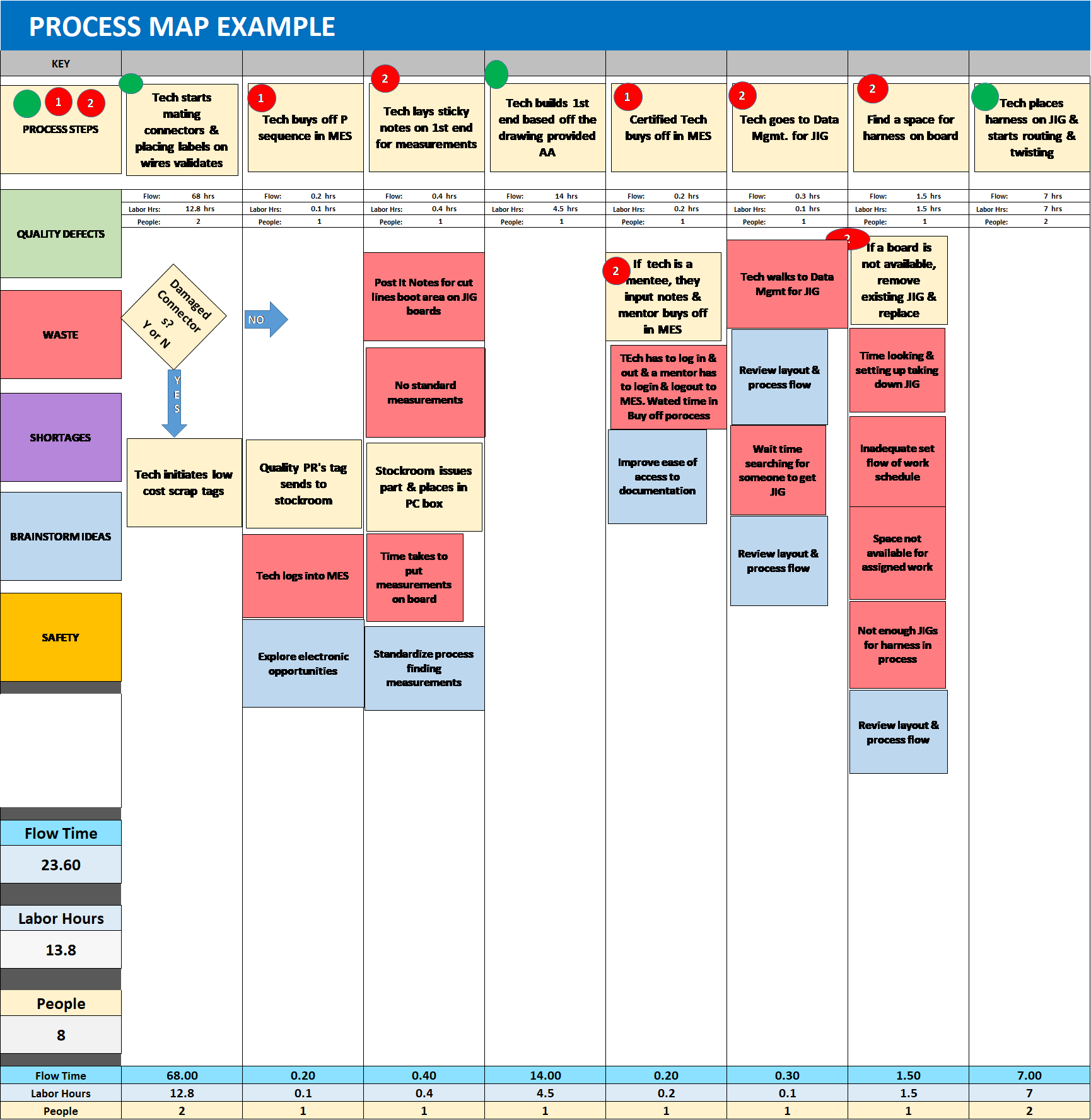
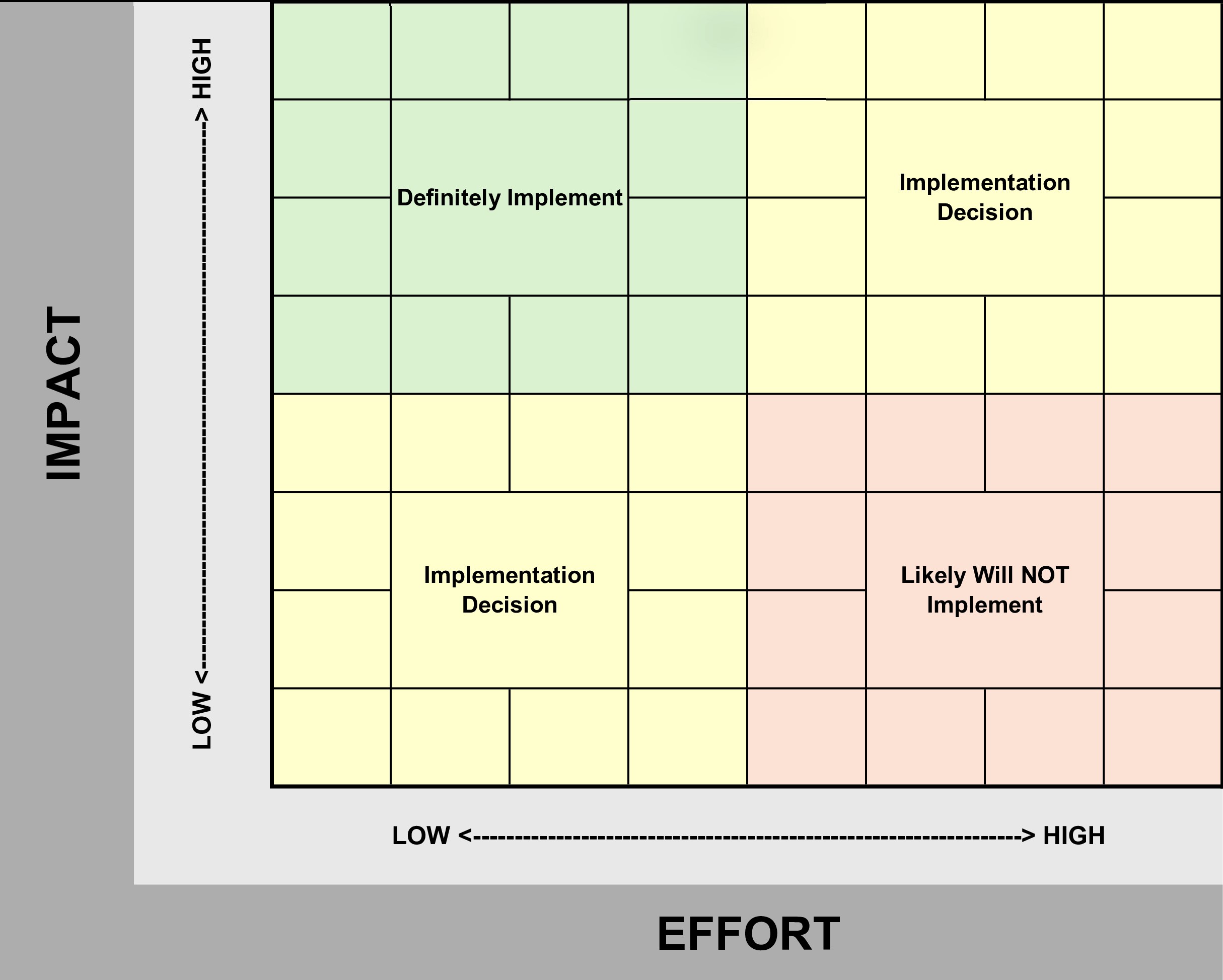
Conclusion:
DMAIC offers a simple but effective way to map a process and analyze wastes to improve key performance metrics within a build. Using this real world example, see if you can improve one of your processes.
Conclusion:
DMAIC offers a simple but effective way to map a process and analyze wastes to improve key performance metrics within a build. Using this real world example, see if you can improve one of your processes.
Lead Industrial Engineer for Process Improvement Projects
Introduction In the realm of precision engineering, achieving flawless surfaces on metal parts is crucial…
Introduction Medium to high volume manufacturing is characterized by the production of large quantities of…
Introduction In the fast-paced world of manufacturing, efficiency is not just a goal but a…
Introduction to Production Planning In the dynamic world of manufacturing, optimizing production schedules is crucial…
Introduction to Deburr Methods in Manufacturing In the world of manufacturing, precision and quality are…
Introduction to Facility Design and Planning Facility Design is a critical aspect of manufacturing plant…
Introduction to Low Volume Manufacturing Low volume manufacturing (LVM) offers the flexibility to produce specialized,…
Introduction In the competitive landscape of manufacturing, reducing wait times and streamlining operations are pivotal…
Introduction In the world of manufacturing and industrial engineering, precision and efficiency are paramount. Fixtures…
Mastering SMED: Speeding Up Changeovers in ManufacturingSingle Minute Exchange of Dies (SMED) is a lean…
Exploring Maynard Operation Sequence Technique (MOST): A Powerful Time Standard MethodIn today’s fast-paced industrial landscape,…
Welding Process Optimization: Enhancing Manufacturing EfficiencyIn the realm of manufacturing, efficiency is the name of…
5S Sustainment: How to Maintain Long Term 5SI am sure everyone in a production setting…
Let’s Talk Process Map Symbols: Deciphering Symbols for Smooth OperationsHey there! So, you’ve stumbled upon…
Let’s Map It Out: A Beginner’s Guide to Creating a Process Map!Hey there, fellow explorer…
How to Value Stream Map a Machining Process?A Guide to Process Mapping in Machining WorkflowIn…
Driving Continuous Improvement: Overview of the DMAIC FrameworkIn the pursuit of operational excellence and quality…
Steps of 5S Methodology in Manufacturing: A Overview Guide to 5S Steps of 5S Methodology…
Optimizing Manufacturing Facility Design for Efficiency and InnovationIn the ever-evolving landscape of manufacturing, the design…
Leave a Reply