Understanding Fixtures in Machining
Fixtures are specialized tools used to position and hold a workpiece in place during machining operations. They are designed to ensure that the workpiece remains steady, allowing for precise cuts and finishes. Fixtures can be categorized into two main types:
- External Fixtures: These hold the workpiece from the outside, typically clamping or securing it from the exterior.
- Internal Fixtures: These hold the workpiece from the inside, often expanding to grip the interior surfaces.
The Role of Fixtures in Manufacturing
- Precision and Accuracy: Properly designed fixtures ensure that the workpiece is held in the exact position required for precise machining.
- Efficiency: Fixtures allow for faster setup times and consistent results, leading to increased productivity.
- Safety: Securely held workpieces reduce the risk of accidents and improve overall safety in the machining process.
- Consistency: Fixtures enable repeatability, ensuring that each part produced meets the same specifications.
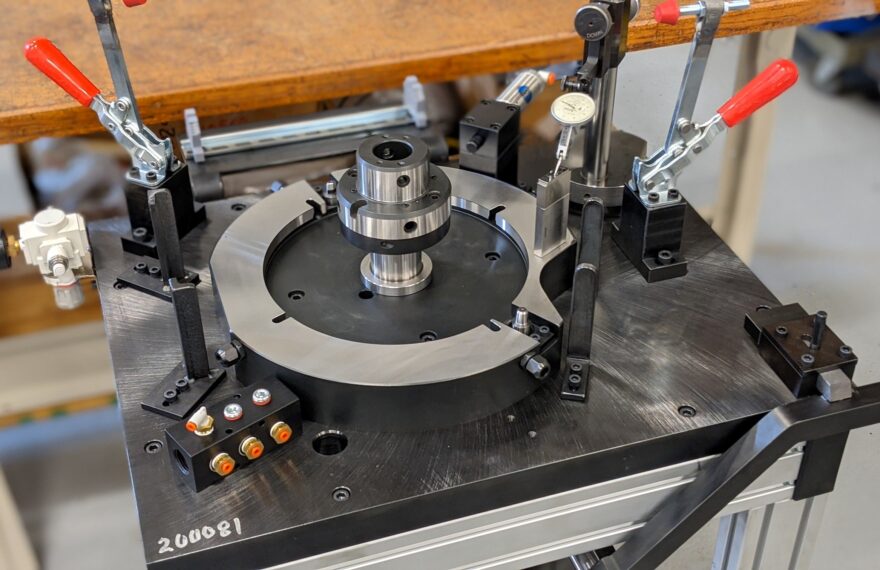
Creating External Fixtures
External fixtures are designed to clamp or hold the workpiece from the outside. Here’s a step-by-step guide to creating an external fixture:
1. Analyze the Workpiece
- Geometry: Understand the shape and dimensions of the workpiece.
- Material: Consider the material properties, such as hardness and brittleness.
- Tolerance: Determine the required tolerances for the machining process.
2. Design the Fixture
- Clamping Mechanism: Choose an appropriate clamping mechanism (e.g., mechanical clamps, hydraulic clamps).
- Base Plate: Design a sturdy base plate to mount the fixture.
- Locators: Incorporate locators to position the workpiece accurately.
- Materials: Select durable materials for the fixture that can withstand the machining forces.
3. Prototype and Test
- Prototype: Create a prototype of the fixture.
- Testing: Test the fixture with the actual workpiece to ensure it holds securely and maintains precision.
4. Optimize the Design
- Feedback: Gather feedback from machinists and engineers.
- Improvements: Make necessary adjustments to enhance the fixture’s performance.
Creating Internal Fixtures
Internal fixtures grip the workpiece from the inside, often expanding to fit the internal surfaces. Here’s how to create an internal fixture:
1. Analyze the Workpiece
- Internal Geometry: Understand the internal shape and dimensions.
- Material: Consider the material properties.
- Tolerance: Determine the required tolerances for the machining process.
2. Design the Fixture
- Expansion Mechanism: Choose an expansion mechanism (e.g., collet chucks, mandrels).
- Base Plate: Design a base plate to mount the fixture.
- Locators: Incorporate internal locators to position the workpiece accurately.
- Materials: Select durable materials for the fixture that can withstand the machining forces.
3. Prototype and Test
- Prototype: Create a prototype of the fixture.
- Testing: Test the fixture with the actual workpiece to ensure it holds securely and maintains precision.
4. Optimize the Design
- Feedback: Gather feedback from machinists and engineers.
- Improvements: Make necessary adjustments to enhance the fixture’s performance.
Integration with Industrial Engineering
Industrial engineering principles are integral to the design and implementation of machining fixtures. Here’s how they tie in:
1. Process Optimization
Industrial engineers focus on optimizing processes to reduce waste and improve efficiency. The design and use of fixtures are critical in minimizing setup times and ensuring consistent quality.
2. Quality Control
Ensuring high-quality output is a primary goal in manufacturing. Industrial engineers use statistical process control (SPC) and other quality control methods to monitor and maintain the performance of fixtures.
3. Ergonomics and Safety
Industrial engineers consider ergonomics to design fixtures that are easy to use and reduce operator fatigue. Safety is also paramount, and well-designed fixtures help prevent accidents and injuries.
4. Cost Efficiency
Effective fixture design can significantly reduce machining costs by improving cycle times and reducing rework. Industrial engineers analyze cost-benefit aspects to ensure that the investment in fixture design yields substantial returns.
Conclusion
The creation of external and internal fixtures is a critical aspect of machining, directly impacting precision, efficiency, and safety. By integrating industrial engineering principles, manufacturers can optimize the design and use of fixtures, leading to improved productivity and quality. As the manufacturing industry continues to evolve, the synergy between machining and industrial engineering will play a pivotal role in driving innovation and efficiency.
Leave a Reply